Case History
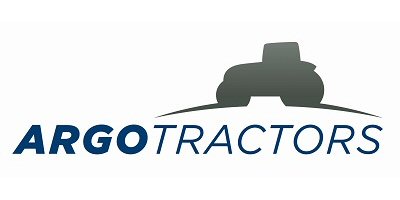
Via Matteotti, 7,
42042 - Fabbrico - RE
Tel: +39 0522 656111
www.argotractors.com
Argo Tractors Spa
Mechanische Industrie, Automobil und Montage
Argo Tractors Spa mit Sitz in Fabbrico (Reggio Emilia) wurde mit dem Ziel gegründet, die Marken und alle Traktoraktivitäten des Argo-Konzerns in sich zu vereinen.
Heute ist Argo Tractors mit seinen Traktoren der Marken Landini, McCormick und Valpadana weltweit präsent und verfügt über eine der umfangreichsten Produktpaletten, die von 35 bis über 300 PS in den Familien der 3-, 4- und 6-Zylinder-Traktoren für das Freiland, den Obstbau, den Weinbau, die Raupen, die Nutzfahrzeuge und die Isodiameter reichen.
Logistische Erfahrung
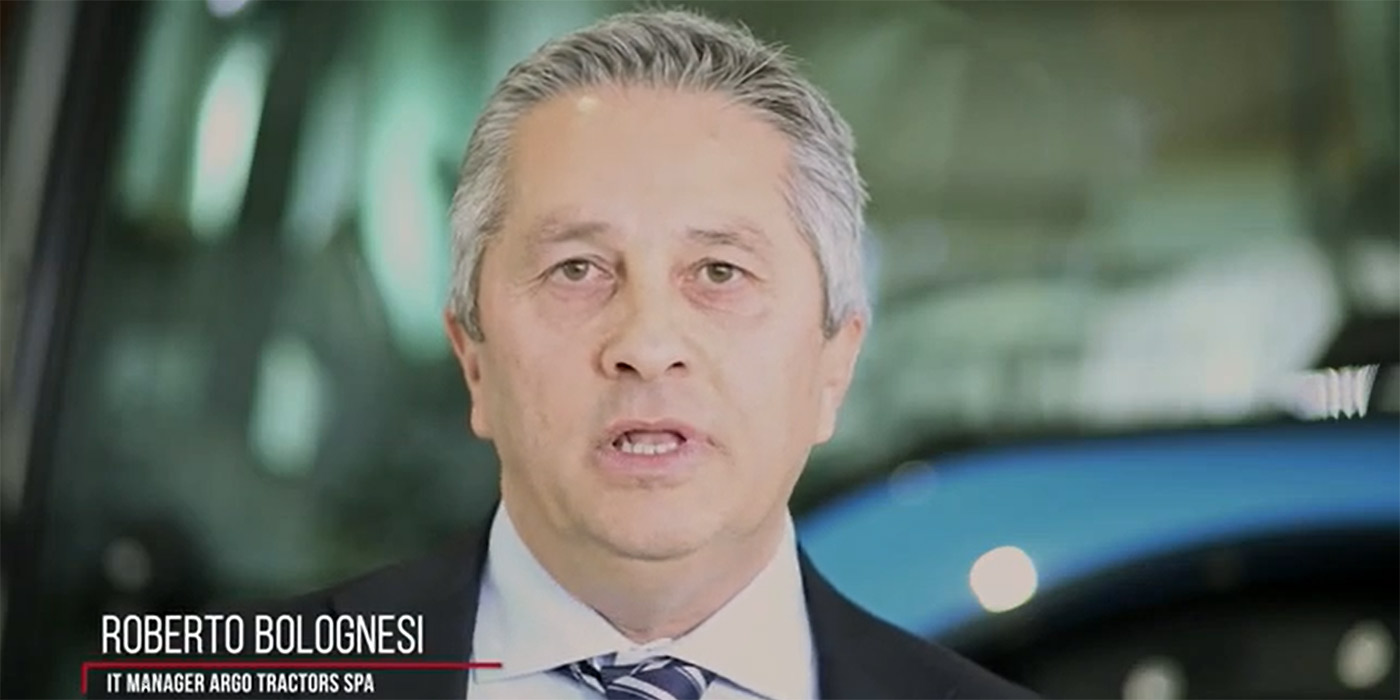
Logistische Erfahrung - Argo Tractors
Interview mit Roberto Bolognesi
Betrieb und Lagerlogistik
Argo Tractors
Die Nummern von Argo Tractors
Argo Tractors bedeutet Landini, McCormick und Valpadana; international bekannte Marken, die einen wesentlichen Beitrag zur Entwicklung der Landtechnik geleistet haben.
Argo Tractorszählt in der westlichen Welt zu den wichtigsten Akteuren der Traktorenindustrie und verfügt über eine perfekt organisierte Lagerlogistik.
PRODUZIERTE TRAKTOREN
PRODUKTIONSANLAGEN
ERSATZTEIL-SERVICEZENTREN
HANDELSFILIALEN