Case History
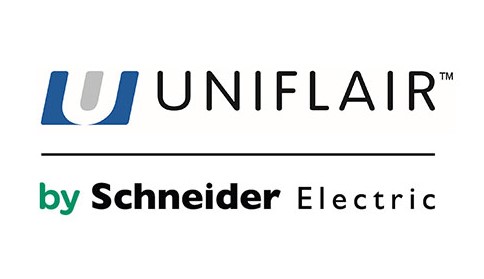
Viale della Tecnica, 2, 35026 - Conselve - PD
+39 049 5388211
+39 049 5388212
www.schneider-electric.com
Uniflair Spa
Mechanische Industrie, Elektrotechnik und Elektronik
Seit 1988 hat sich Uniflair auf die Entwicklung, Herstellung und Vermarktung von Präzisionsklimageräten, Kühlsystemen und Doppelböden spezialisiert, die fortschrittliche und zuverlässige technologische Lösungen für das Bauwesen, Telekommunikations- und Internetsysteme sowie industrielle Kühlung und Komfort bieten.
Die Expansion von Uniflair begann auf dem heimischen Markt und hat Europa und andere Kontinente erreicht. Derzeit ist Uniflair in mehr als 60 Ländern der Welt mit eigenen Niederlassungen und über ausgewählte Partner vertreten.
Die Uniflair-Organisation gliedert sich in den Hauptsitz in Conselve (Padua), den Produktions- und F&E-Standort, in Büros in Mailand, Rom und Neapel sowie in Niederlassungen in Spanien, Deutschland, Ungarn, Südafrika, Indien und China.
Schneider Electric
Die Nummern von Schneider Electric
Schneider Electric, ehemals Uniflair, ist auf die Entwicklung, Herstellung und Vermarktung von Präzisionsklimageräten, Kühlsystemen und Doppelböden spezialisiert, die fortschrittliche und zuverlässige technische Lösungen für Gebäude, Telekommunikations- und Internetsysteme sowie industrielle Kühlung und Komfort bieten.
MITARBEITER
PRODUKTIONLINIEN
PRODUKTIONANLAGE WELTWEIT
UND MEHR LÄNDERN
Logistics Experience
CONSELVE (PD) PLANT
- 16,000 m2 production area
- 14 production lines
- 6500 pallet places
- 1000 m2 of racking
PLANTS IN THE WORLD - St. Louis R&D Center (USA)
- Costa Mesa Plant (USA)
- Bangalore Plant R&D Center (INDIA)
- Zhuhai (China)
- Shanghai R&D Center - China