Case History
Einsteinstraße
I-39100 Bozen (BZ)
+39 0471 553500
info@woerndle.it
https://www.granchefpremiumfood.it/
FILIALI
Standort Percha
Zum Hohen Kreuz, 5
I-39030 Percha (BZ)
-
Standort Castenedolo
Via Vulcania, 31
I-25014 Castenedolo (BS)
Wörndle Interservice GmbH
Logistics & Transportation, Food & Beverage
Woerndle Interservice is a company that has specialized for more than 50 years in the distribution of high-quality kitchen products: fresh, ultra-fresh, dried, frozen, and more, designed to meet the needs of every restaurant and hotel.
Recognized in the market under the GranChef brand, every day it receives products from selected suppliers from Europe, America, Asia, and Australia and prepares and ships them to more than 6,000 customers throughout the country for delivery within 24 hours.
Logistics Experience
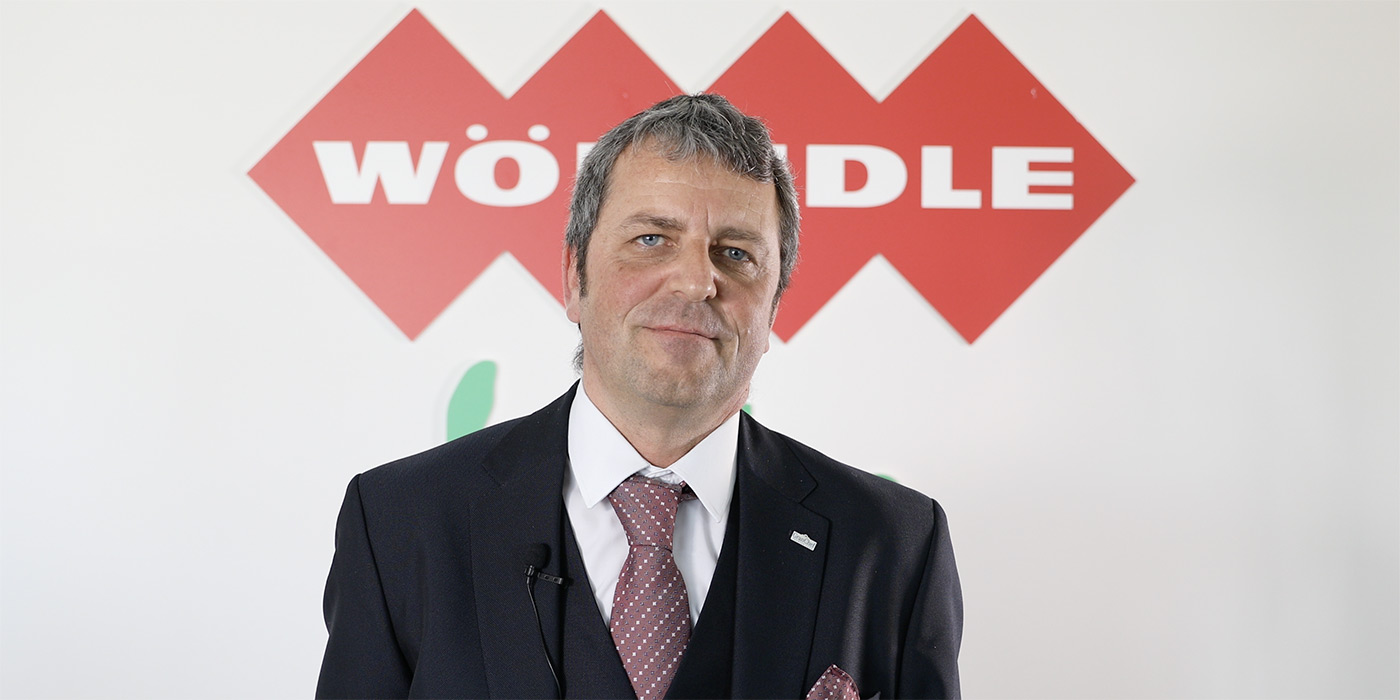
Logistics Experience - Wörndle Interservice
Interview with Roman Tschimben
The numbers of Wörndle Interservice
The partner for haute cuisine in Italy.
Wörndle Interservice has specialized for over 50 years in the distribution of products for high catering.
PEOPLE
PRODUCTS
ACTIVE CLIENTS
MM. TURNOVER
LOGISTICS CENTRE
In October 2021 Wörndle Interservice inaugurated a new logistics centre in Castenedolo (BS), from where it is able to serve the entire Italian market.
Product management:
- References: ca. 8,500
- Orders: over 2,000/day
- Picking: 9,000 lines of order/day
The Castenedolo plant is structured as follows:
- total surface: 31,500 sqm
- covered area: 11,355 sqm
- refrigerated area: 6,300 sqm
- frozen area (-20°C): 2,400 sqm
- loading/unloading bays: 16
- Pallet places on shelf: 8,500