What is WorkForce Management System? And Labor Management System?
Why is it useful to adopt a Workforce Management Software?
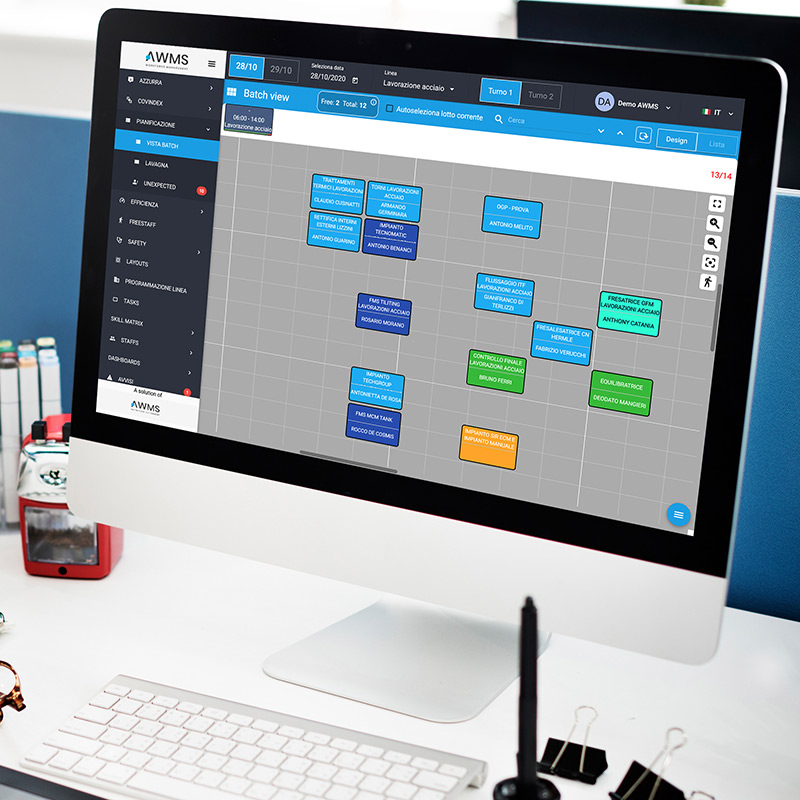
- COST REDUCTION: Enables better planning of blue collars, based on demand with a 33% reduction in unplanned overtime costs.
- PRODUCTIVITY INCREASE: 75 % Time reduction for employee scheduling management. By assigning the right person to the right place, the production system becomes more efficient, with an average increase in productivity of +4%.
- REAL TIME DATA VIEW: IT allows all blue collar-related information to be in a single repository, updated in real time, capitalizing the information.
- CORPORATE SOCIAL RESPONSABILITY: adopting WFM platforms means humanizing the warehouse by valuing people through respecting employees and developing their skills.
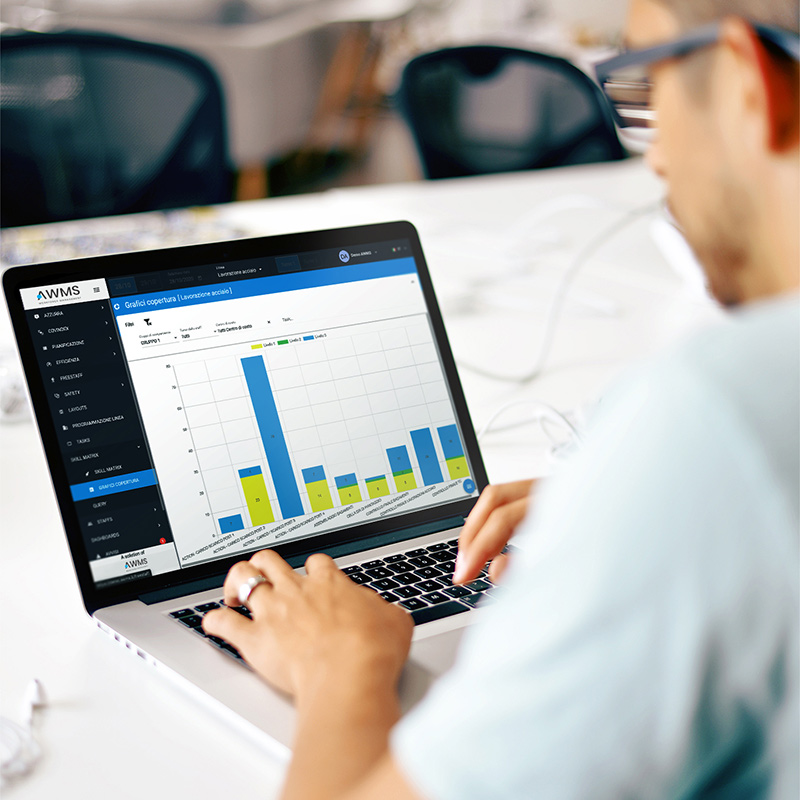
- REDUCTION IN USE OF PAPER: the entire planning is managed by the software. -100% use of paper and other non-integrated systems
- INCREASE IN PROFESSIONAL SATISFACTION: greater involvement of factory staff due to increased transparency and better communication with team leader (i.e. reduced absenteeism and turnover) +11% job satisfaction
- RESPECT OF COMPLIANCE: the entire planning is carried out in full compliance with current compliance reducing the risk of accidents and work-related diseases.
How does a WorkForce Management System work?
Funzioni principali gestite
- PLANNING: AWMS provides a visual and intuitive tool to plan workers in individual workstation based on their availability, competence and physical limitation, updated in real time. Employee work can be monitored through interactive layouts for each activity performed for a short and/or long period and best allocate your resources in each area.
- SCHEDULING: AWMS Scheduling allows for efficient, simple and immediate planning of work shifts. By collecting and cross-referencing data on production needs, workforce availability, and contractual constraints, AWMS suggests an ideal shift plan and the most appropriate workers to cover it. The system also considers labor legislation and regulations, company rostering rules, and fair treatment rules in addition to employee preferences. AWMS integrates data from systems dedicated to production management and scheduling, thus ERP, MES, and Schedulers, with those from HR administrative management into a single shared working tool.
- EFFICIENCY: Through a dynamic and intuitive report, AWMS calculates and provides the level of efficiency for each operator and cost center. Efficiency is calculated on the basis of the hours performed by department and the hours surrendered or lent for each operator in relation to their cost center.
- SKILL MATRIX AND CERTIFICATIONS: The dynamic skill matrix of AWMS automatically updates operators' skills based on the activities performed during the day, coding them according to different levels. In case of competence advancement, AWMS sends an alert to the team leader, requesting an approval. Moreover, AWMS digitalizes and traces the initial training and specific certifications for machine use. Finally, through its dashboard analytics it offers an immediate overview on competence gaps, on the basis of which it makes suggestions on actions to be taken.
- ABSENCE MANAGEMENT: AWMS provides a comprehensive overview of staff absences, with the ability to break them down by type and view staff absenteeism in absolute value and percentage day by day. The platform records absence history for both the individual worker and the entire department. In addition, by accessing the calendar view you can have a complete and immediate overview of operators' vacation availability over the year. A list of operators who have not shown up for work allows you to align HR Manager and Production on the unexpected in real time and manage them quickly and efficiently through immediate replacement of staff, chosen on the basis of the skills matrix.
- SAFETY: The Safety module allows to plan staffing based on each worker's contraindications, prescriptions and physical limitations, correlating them with the risk of the workstations. In addition, AMWS protects your company from the Covid-19 pandemic. By calculating and monitoring the Convindex risk index, AWMS allows you to protect workers and prevent possible outbreaks.