Case History
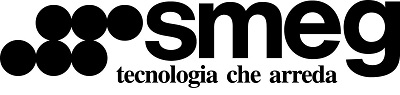
Via Leonardo da Vinci, 4, 42016 - Guastalla - RE
+39 0522 8211
+39 0522 821452
smeg@smeg.it
www.smeg.it
Smeg Spa
Mechanische Industrie, Möbelzubehör und Bauwesen
Insbesondere bei der Produktkontrolle mussten Fehler bei der Annahme, Lagerung, Kommissionierung und beim Versand beseitigt werden. Die verantwortlichen Mitarbeiter mussten auch ihre Arbeitsweise ändern und die Zuordnung der Waren sofort bekannt geben, die Wege und Leerfahrten von Wagen und Geräten verringern und die Unterbrechung des normalen Lagerbetriebs zur Durchführung von Papierinventuren vermeiden.
Matteo Bertolotti
Logistics and Production Manager Smeg
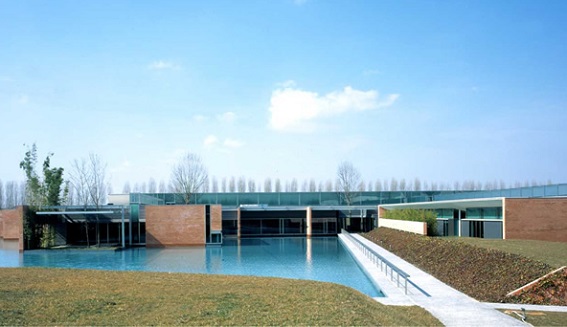
Die Firma
Smeg, eine globale Marke
Smeg ist ein italienischer Haushaltsgerätehersteller mit Sitz in Guastalla, in der Provinz Reggio Emilia.
Smeg hat weltweit Tochtergesellschaften, Vertretungen und ein umfangreiches Händlernetz.
Die Smeg-Gruppe ist dank einer Unternehmenskultur, die einen extremen Fokus auf die Qualität, den technologischen Inhalt und das Design ihrer Produkte legt, international als Spitzenreiter des Made in Italy anerkannt.
Die Lösungen von Replica Sistemi
Bevor Smeg sich an Replica Sistemi wandte, verwaltete das Unternehmen seine Lagerprodukte durch manuelle Dateneingabe mit Hilfe eines Verwaltungssystems. Die unterschiedlichen Bedürfnisse von Smeg bei der Verwaltung seiner Lager und der Qualitätskontrolle erforderten ein flexibles System. StockSystem konnte sich durch Parametrisierung an alle Lagertypen zur Beschickung der Produktionslinien anpassen und so die Verwaltung der Lagerflüsse effizienter gestalten. StockSystem hat es Smeg durch die Qualitätskontrolle ermöglicht, weiterhin die hohen Produktionsstandards zu gewährleisten, die seit jeher die Philosophie des Unternehmens ausmachen.
ZIELE DES PROJEKTS
- Beseitigung von Fehlern bei Annahme, Lagerung, Kommissionierung und Versand;
- Erhöhung der Geschwindigkeit und Effizienz bei der Auftragsabwicklung,
- die Zuteilung von Waren sofort bekannt zu machen;
- zentrale Kontrolle der Lageraktivitäten und des Wissens, insbesondere in der Warenverwaltung.
PROBLEME
- Inhomogene Werkstoffe (Bauteile, MEC- und SMA-Halbzeuge, kältetechnische Komponenten).
- Qualitätskontrolle.
- Verfügbarkeit der Kommissionierung zum Zeitpunkt der Einlagerung.
- Drei verschiedene Lagertypen.