Case History
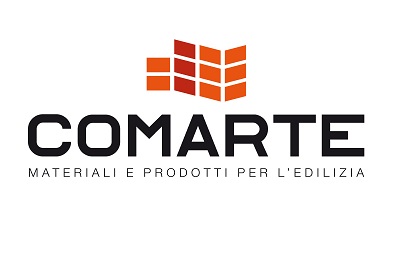
Via G. Di Vittorio, 74/76
46020 - Pegognaga - MN
Tel: +39 0376 558432
magazzino.pegognaga@comarte.it
www.comarte.it
Co.M.Art.E Soc. Coop.
Furniture Complements & Construction
COMARTE owes its name to the CONSORZIO MANTOVANO ARTIGIANI EDILI AND AFFINI. After 45 years, COMARTE ranks among the top 30 companies in ITALY in terms of size and sales volume.
Co.M.Art.E
CO.M.Art.E's numbers
An acronym for Consorzio Mantovano Artigiani Edili e Affini (Mantuan Consortium of Building and Related Craftsmen), it is a Consortium that operates as a Warehouse-Retailer of building materials and products.
AND MORE CLIENTS AND PARTNERS
MLN AND MORE OF SOLD UNITS
MANAGED REFERENCES
Company
Watch the video