Case History

Via Provinciale 5/7/9, 83030 - Manocalzati - AV
Tel: +39 0825 620111
info@capaldo.it
portale.capaldo.it
Antonio Capaldo Spa
Ferramenta & Idraulica
L'Azienda, fu fondata nel 1935 ad Atripalda dove ha conservato la sede legale fino al luglio del 2013, quando la sede legale è stata unificata con la sede operativa di Manocalzati.
Nel 1984 la sola sede operativa fu trasferita nel limitrofo territorio del Comune di Manocalzati, in un complesso di nuova costruzione costituito da due grandi capannoni con palazzina uffici ed ampi parcheggi.
Successivi ampliamenti realizzati negli anni 1992-1994 e 2000-2001 hanno consentito di raggiungere le dimensioni attuali del complesso che sorge su di un'area di proprietà di circa 80.000 mq. entro la quale insistono costruzioni per oltre 40.000 mq. coperti.
La necessità di razionalizzare e potenziare la logistica aziendale suggerì di realizzare un impianto automatizzato: e così negli anni 2006-2009 fu costruito, nel Nucleo Industriale di Avellino - località Santorelli - su di un'area di proprietà di circa 70.000 mq., un insieme di magazzini capaci di ospitare merci per un volume complessivo di mc. 400.000.
Il magazzino automatizzato dedicato ai pallet ne ospita ben 40.000 ed è alto 33 mt. Allo stesso modo, negli anni, si è arricchita la gamma merceologica. Alla iniziale e classica "Ferramenta e Colori " ben presto si aggiunsero i " vetri in lastre" ( da tempo dismessi ) e poi altre categorie merceologiche.
Logistics Experience
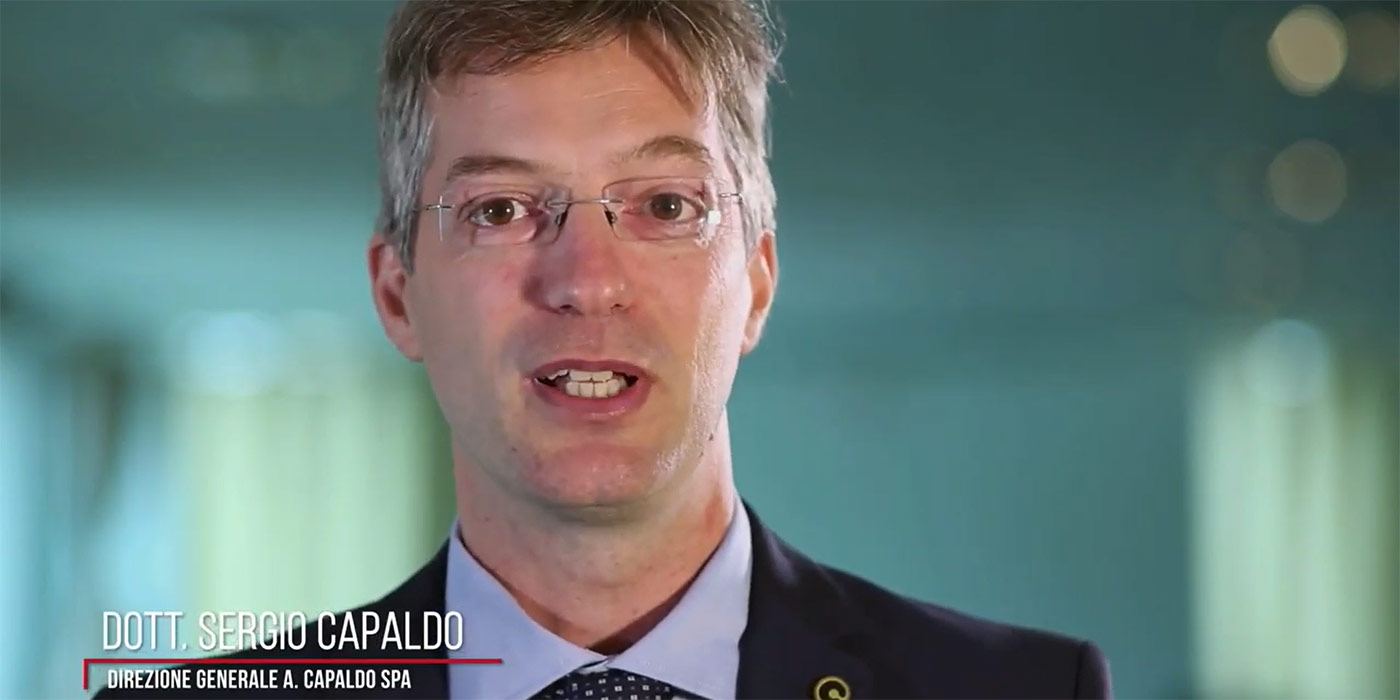
Logistics Experience - A. Capaldo
Intervista a Sergio Capaldo
A. Capaldo SpA
I numeri di A. Capaldo SpA
A. Capaldo Spa, fondata ad Atripalta (AV) nel 1935, è oggi leader in Italia nella distribuzione di ferramenta, utensileria, prodotti per l’edilizia, arredo garden etc.
METRI QUADRI MAGAZZINO
REFERENZE GESTITE
POSTI PALLET
PALLET IMMAGAZZINATI ALL'ORA
CASSETTE IMMAGAZZINATE ALL'ORA
CASSETTE STOCCAGGIO
ESIGENZE
Nel 2005 c’erano 18.000 articoli a catalogo che spaziavano dalla minuteria al voluminoso forniti da oltre 1.000 fornitori nazionali ed esteri per una movimentazione complessiva di 600 TEU/anno.
Ogni giorno venivano evase circa 200 consegne ad un totale di oltre 3.000 clienti attivi ai quali era garantito anche il servizio di riparazioni. Lo stoccaggio avveniva in modo tradizionale e la gestione del magazzino era con «carta e penna».
Le problematiche principali erano:
- magazzini complessi con tipologie di prodotto molto diverse;
- magazzini diversificati:
- due magazzini per vendita al dettaglio, per un totale di 10.000 metri quadrati per il picking e per vendita all’ingrosso;
- un magazzino di 40.000 metri quadrati per il picking e scorta di prossimità;
- un deposito con 40.000 posti pallet per scorta fuori stagione e riserva materiale;
- un deposito di 8.000 metri quadrati per gestione delle scorte;
- inefficienze operative in magazzino;
- ricerca di soluzioni software per la gestione di tutte le attività di magazzino.
SOLUZIONI
Il management della Capaldo ha preso coscienza di alcune inefficienze operative di magazzino e, dopo un’accurata software selection, ha deciso di affidare al warehouse management system StockSystem la gestione di tutte le attività operative e decisionali.
L’azienda ha quindi implementato la soluzione StockSystem nella versione standard, coi terminali RF che permette di trasmettere in tempo reale i dati al sistema di gestione del magazzino. Gli operatori addetti alla logistica lavorano con efficienza utilizzando terminali RF (Radiofrequenza) interfacciati con ripetitori remoti Access Point.
Gli obiettivi erano:
- crescita: in termini sia di numero delle referenze gestite sia dei volumi;
- riduzione degli errori;
- aumento della produttività e riduzione del lead time;
- maggiore flessibilità operativa (gestione delle personalizzazioni);
- movimentazioni in tempo reale e informazioni "everywhere";
- certezza dei tempi e degli operatori;
- gestione puntuale dei rifornimenti tra magazzini;
- gestione puntuale dei rifornimenti tra ubicazioni dello stesso magazzino;
- interrogazioni di magazzino real-time;
- rintracciabilità dei materiali;
- efficienza nell’utilizzo degli spazi di magazzino;
- semplificazioni nella gestione dell’inventario rotativo.
StockSystem inizialmente si interfacciava all’ERP AS/400 già in uso dall’azienda e avendo constatato la professionalità del team di Replica Sistemi decide di cambiare partner per il sistema informativo ed affidarsi a Replica Sistemi anche per la gestione dell’ERP.