Case History
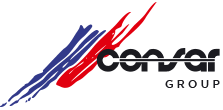
Via Vicoli, 93, 48124 - Ravenna
+39 0544 469111
+39 0544 469243
Consar Soc. Coop. Cons.
Logistics & Transportation
Con.S.A.R. Soc. Coop. Cons. is a freight forwarding company established in 1960, which now operates in all segments of freight handling.
The headquarters is located within a logistics park that provides services for vehicle washing, parking, columns with electrical outlets for refrigerated vehicles, fuel dispensers*, workshop, bar-restaurant, offices of the main trade associations (CNA, CONFARTIGIANATO) and Unipol insurance agency, all within a modern site that is continuously monitored.
In 1993 it obtained certification of its Quality System UNI EN ISO 9001:2000, a certification that was supplemented with SQAS in 1999.
Consar Logistics Services
Consar Logistics Services' numbers
Logistics operator active in all segments of goods handling, with centralized operations at the Ravenna HUB, where flows destined for storage, handling and distribution of goods converge.
TOTAL SQM
SQM CONTROLLED TEMPERATURE
LOADING/UNLOADING BAYS
PALLET SPOTS
Facilities
- an area of about 20,000 m2 for the storage of conventional product in open-floor stacks ("White goods" warehouse)
- an area of about 2,500 m2 with controlled temperature (from + 4° to + 12°) in which primary and finished food products, as well as special products, are stored in special optimized "DRIVE IN" system with about 2,500 track racks
- a 10,000 m2 shelved area for storage of food products (with relevant HACCP authorization) and industrial products such as packaging and the like. Groupage filling and container emptying activities are also carried out in this area
- an area of 10,000 m2 managed by the subsidiary LOGIKEM, for the storage of phytopharmaceuticals and dangerous goods under ADR regime, with particular attention to the emerging market of imported phytopharmaceuticals and plant protection products, which has its natural outlet in the port district of Ravenna
We chose Replica Sistemi because StockSystem is a standard software application that is highly flexible and adaptable to the different types of goods handled in our warehouses: white goods, food and industrial products, phytopharmaceuticals and dangerous goods. In addition, it is fully integrated with the information system, so our customers can know in real time their inventories and the status of their shipments.
Andrea Rosetti
Information Systems Manager Consar Group
NEEDS
In the two-year period since 2002, the management of Consar Servizi Logistici decided to improve some aspects of the logistics process to optimize the organization and management of all logistics flows managed in its warehouses: goods entry, storage, internal handling, picking and inventory, to improve the service offered to its customers.
The goals were:
- increased performance
- increased accuracy and efficiency
- inventory security
- product serial number traceability
- copacking, assembly, and palletizing
- cross docking
- returns and warranty management
- tracking/traceability
- cyclic inventories
- FIFO and LIFO
- order backlog management
- order formation
- order grouping
- parcel labeling with bar codes
- mixed packages composition with related packing list
- product configuration
- reliability certifications and statistics decrease in errors
- improvement of customer service
SOLUTIONS
After careful evaluation, Consar Logistic Services decided to implement Replica Sistemi's StockSystem solution in the standard version, with RF terminals.
The project was structured by identifying a figure within the company who, together with Replica Sistemi's project manager, carried out all the analyses relating to warehouse layout, types of materials, incoming and storage flows, picking and shipping flows and integration with the central information system.
In particular, the following were carried out:
- testing of each individual function on an updated DB
- meetings with warehouse operators (especially in the last month before installation)
- identification of the start date