Case History
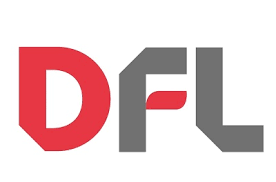
Via Santa Maria degli Ulivi, 1
84036 - Sala Consilina - SA
Tel: +39 0975 45524
info@nuovadfl.it
www.nuovadfl.it
DFL Srl
Hardware & Plumbing
The DFL company today represents one of the most evolving businesses in our area.
Founded in Sala Consilina as a retail outlet for hardware, building materials and related items, over the years it has grown in many ways, becoming a hardware wholesaler as well as a point of reference for all local retailers and the entire Campania region.
Thanks to a sound business organization it has managed, quickly, to expand its sales outside the region as well, achieving important goals and satisfactions in many areas of southern Italy.
Integrated technologies:
Company
Watch the video
The DFL company today represents one of the most evolving businesses in our area.
Founded in Sala Consilina as a retail outlet for hardware, building materials and related items, over the years it has grown in many ways, becoming a hardware wholesaler as well as a point of reference for all local retailers and the entire Campania region.