Case History
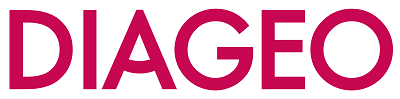
Strada Statale, 63/65
12069 - Santa Vittoria d'Alba - CN
Tel: +39 0172 477111
Diageo Operations Italy Spa
Food & Beverage
Diageo Operations Italy Spa
Diageo's global numbers
Diageo is among the leading players in the premium alcoholic beverage industry, was formed in 1997 by the merger of two major players in the industry, England's Grand Metropolitan Plc and Ireland's Guinness Plc.
BRANDS
PRODUCTION SITES
COUNTRIES IN THE WORLD
EMPLOYEES
Company
Watch the video
The Group operates in our country through two companies: Diageo Italia SpA, based in Turin, which is responsible for the marketing and distribution of the brands in its portfolio, and Diageo Operations Italy, based in Santa Vittoria d'Alba, Cuneo, which is one of the most important production centers at the European level.
Ninety-seven percent of the entire volume originated at the Santa Vittoria facility is destined for export, as part of a large market whose main destination is Great Britain (56 percent).