Case History
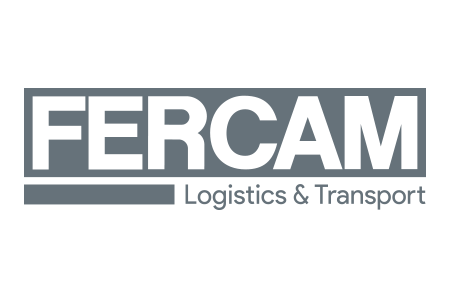
DACHSER & FERCAM ITALIA SRL a socio unico
Logistics & Transportation
In over 65 years of history, Fercam has grown from a small local carrier to one of Europe's Leaders in integrated logistics.
DACHSER & FERCAM ITALIA SRL
The Logistics Management numbers
Logistics & Transport: in one word… DACHSER & FERCAM ITALIA
BRANCHES
COLLABORATORS
LOADING UNITS
SQUARED METERS OF LOGISTICS SURFACE
Fercam - Logistics Management
Watch the video
In more than 65 years of history, FERCAM has grown from a small local carrier into one of Europe's leading logistics operators: an evolution that started with full-load transport by road and rail, moving through national and international road shipments to air and sea shipments, consolidating through the opening of numerous and vast logistics centers that today represent the flagship of our offer.