Case History
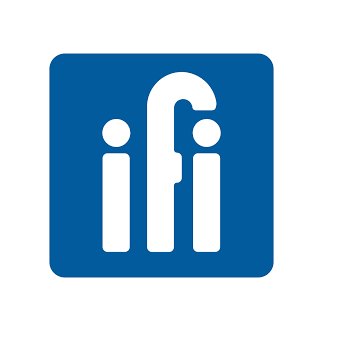
Strada Selva Grossa, 28/30,
61010 - Tavullia - PU
Tel: +39 0721 20021
info@ifi.it
www.ifi.it
Ifi Spa - Industria Frigoriferi Italiana
Mechanical industry, Furniture Complements & Construction
Ifi is a leading company in innovative design and technology solutions in public venue furniture.
Founded in Pesaro in 1962 as an artisan company specializing in the production of bar furniture, IFI marks the history of the industrial bar counter, thanks to the constant innovations that, time after time, have dictated new reference standards for the sector.
Today the company continues to consolidate its role as a leader in the public venue furniture sector, with more than 3,000 installations each year.
We looked for a partner for the renewal and rationalization of logistics processes in manufacturing. We can say that we found it in Replica Sistemi: from the very first steps it has been by our side and the strategic goal of computerizing the factory has been achieved.
We have significantly improved the Gross Operating Margin.
Eng. Davide Pezzi, Mirko Vichi
Operations Director INDUSTRIEIFI, entry Logistics Manager
Company
Watch the video
Founded in Pesaro in 1962 as an artisan company specializing in the production of furniture for bars and ice cream parlors, IFI marks the history of furniture for food & beverage establishments, thanks to innovations that have dictated new standards for the industry, worldwide.