Case History
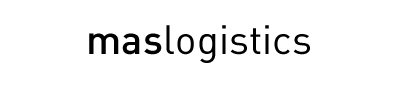
Mas Logistics Srl
Logistics & Transportation, Textile & Fashion
Mas Logistics, a company that manages multiple logistics services in the fashion industry.
It was born out of its entrepreneur's desire to make available in-depth knowledge of operational processes, consolidated through many years of experience at some of the most complex realities in the apparel industry.
It offers management of raw material warehouses, finished product, and key value-added services for the industry.
They are able to solve all problems by adapting to the client's organizational model providing fast and flexible service.
Mas Logistics
Mas Logistics' numbers
Mas Logistics is a company that manages multiple logistics services in the fashion industry.
EMPLOYEES
SQM OF WAREHOUSE
MANAGED LINES
Company
Mas Logistics was born out of the desire of its entrepreneurs to make available a deep knowledge of operational processes, consolidated through many years of experience at some of the most complex realities in the apparel industry.
It offers management of raw material and finished product warehouses and the main value-added services for the industry: ironing, accessory testing, repair and customization of garments.
Needs
In 2006, Mas Logistics management decided to computerize warehouse operations to improve performance, reduce errors, and manage a large number of features for each type of warehouse:
FABRICS AND PIECES
In the fabric and piece warehouse it was important to achieve:
- the matriculation of each individual piece
- quality control
- the management of useful meters and net meters
- the division by sample and production
- the management of fabric testing
YARNS
In the yarn warehouse, it was essential to define
- the management of counts, baths and cottons
- quality control
- the division by sampling and production