Case History
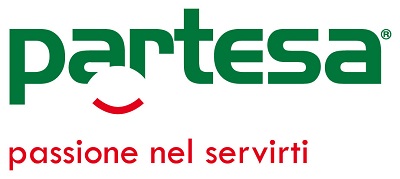
Partesa srl - Emilia Romagna headquarter
Food & Beverage
Partesa is the distribution network specializing in sales, distribution, consulting and training services for the Ho.Re.Ca. channel.
In almost twenty years of history - and more than 60 thousand customers served in Italy - it has achieved maximum distribution capillarity, a careful portfolio of quality products, personalized services and great logistic solidity.
With a particularly innovative approach to the market, "Partesa per il Vino" was born in 1999, a structure to affirm the centrality of the distributor's role even in the quality wine sector and which already boasts a widespread presence in the territory.
Partesa represents a real evolution of the distribution concept, thanks to some factors that distinguish it.
Products:
Integrated technologies:
Partesa srl
Partesa's numbers
Partesa is the distribution network specializing in sales, distribution, consulting and training services for the Ho.Re.Ca. channel.
CUSTOMERS
AUTOVEHICLES
DEPOSITS
REFERENCES
Logistics
Video Case Study Partesa Emilia Romagna
Partesa offers a complete food & beverage distribution service, starting with delivery at the required time and manner.
It constantly invests resources to increase the efficiency and quality of logistics services, to improve safety in warehouses and at consumption points where facilities are installed. It is able to guarantee and sustain a delivery punctuality and completeness rate of 96% despite the large numbers: more than 1 million orders processed each year corresponding to about 23 million packages delivered.