Case History
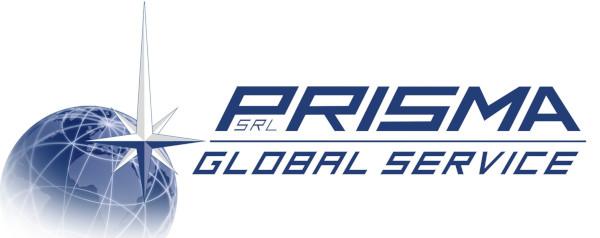
Via Pallone 20, I-37121
Verona
Tel: +39 045 9216611
info@prisma-global-service.net
Prisma Global Service srl
Logistics & Transportation
Prisma Global Service srl was founded in 1989 by a group of partners with a solid experience in international forwarding and is located in the Interporto Quadrante Europa of Verona, the crossroads for logistics and forwarding activities in northern Italy.
Initially the 'business developed in the area of groupage shipments by truck and rail to German-speaking countries, and then turned to other markets and different types of services.
To date they offer services in import/export to and from 22 European and non-European countries in cooperation with 40 correspondents, air and sea freight forwarding, integrated and distribution logistics, customs and consulting services.
Prisma Global Service srl
Logistics
Prisma offers integrated logistics services by making use of adequate human and material resources to meet the most demanding requirements.
Goods are stored in ultra-modern warehouses with customer-dedicated layouts.
TRANSPORTERS
DRIVERS
LOGISTICS WORKERS
Facilities
- 30,000 square meters of modern warehouses equipped with CCTV and double alarm system: cross docking, customs warehouse and VAT warehouse, logistics:
- Interporto Quadrante Europa: 5,000 sq m of covered warehouses, customs warehouse and private VAT warehouse
- Verona Vallese logistics terminal in Oppeano: 10,000 sqm on an area of 20,000 sqm
- Villafontana logistics terminal in Bovolone: 12,000 sq. m. on an area of 20,000 sq. m.
With the aim of offering logistics and shipping services designed to achieve maximum customer satisfaction, we make specific infrastructural and technological investments, including precisely StockSystem, which is the most important one as far as third-party warehousing is concerned.
Stefano Pasinato
CEO Prisma Spa
Needs
In 2000-2001, Prisma's management decided to improve some aspects of the logistics process to improve the organization and management of all logistics flows handled in its warehouses: goods entry, storage, internal handling, picking and inventory, to improve the service offered to its customers.
GOALS
The goals of the restructuring project were:
- increased performance;
- security of inventories;
- traceability of flows; and
- seasonality management
- sample management
- management of accessories
- elimination of the final control phase;
- decrease in errors;
- improved customer service
- increased accuracy and efficiency