Case History
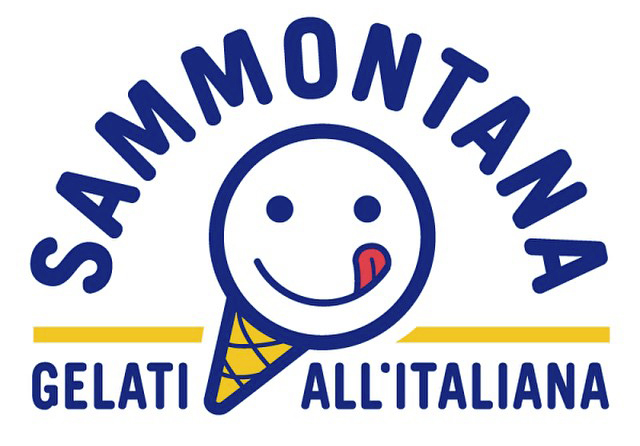
Sammontana Spa
Food & Beverage
Integrated technologies:
Logistics Experience
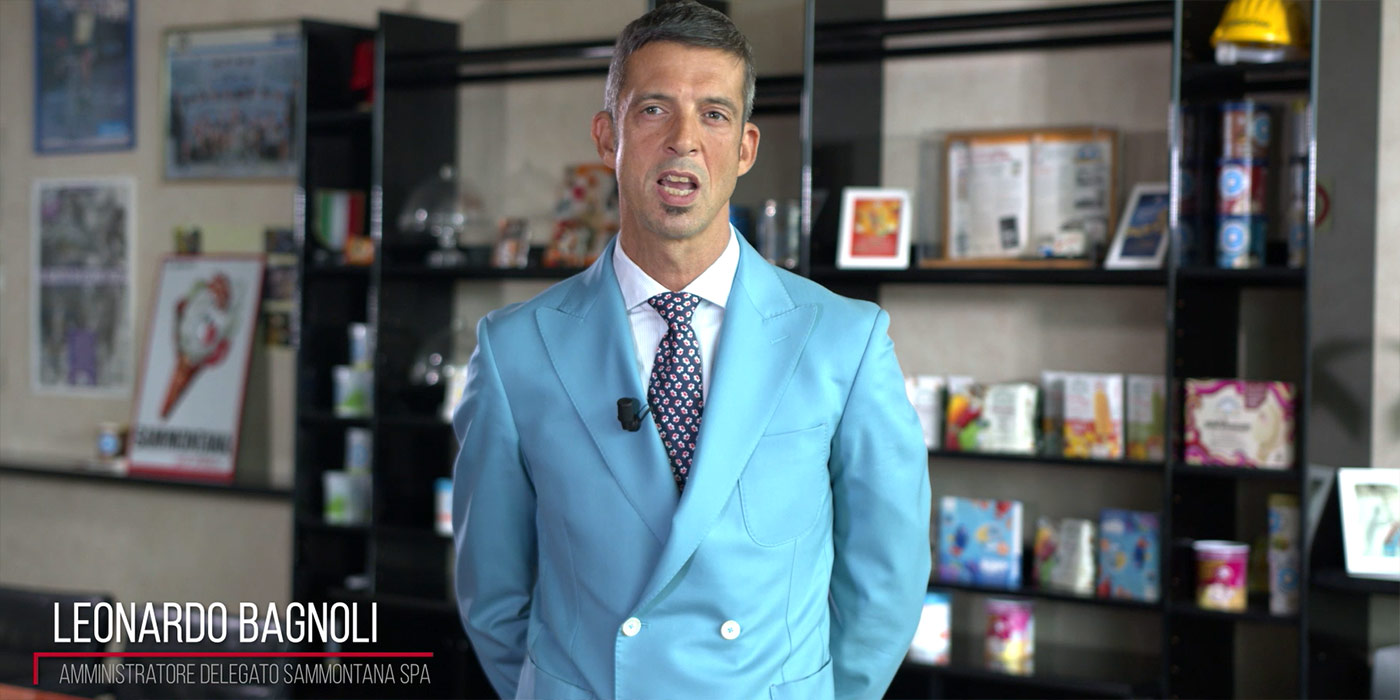
Logistics Experience - Sammontana
Interview to Leonardo Bagnoli
Sammontana
Sammontana's numbers
Sammontana is the largest Italian ice cream producer, and the market leader in frozen croissant.
SERVED CAFÉS
PRODUCTION FACILITIES
BILLION SOLD PORTIONS
+ EMPLOYEES
Company
Sammontana was established in 1946 in a dairy bar in Empoli purchased by the Bagnoli family, which today, as then, owns and runs the company.
It produces and markets the brands Sammontana, TreMarie, Il Pasticcere, Mongelo and Bon Chef.
It offers products with a unique taste, born from intuition, care and passion for quality.
It is a company that has grown alongside customers and helped develop the traditional channel.
It is a reliable and competent partner of modern distribution, serving private label as well.
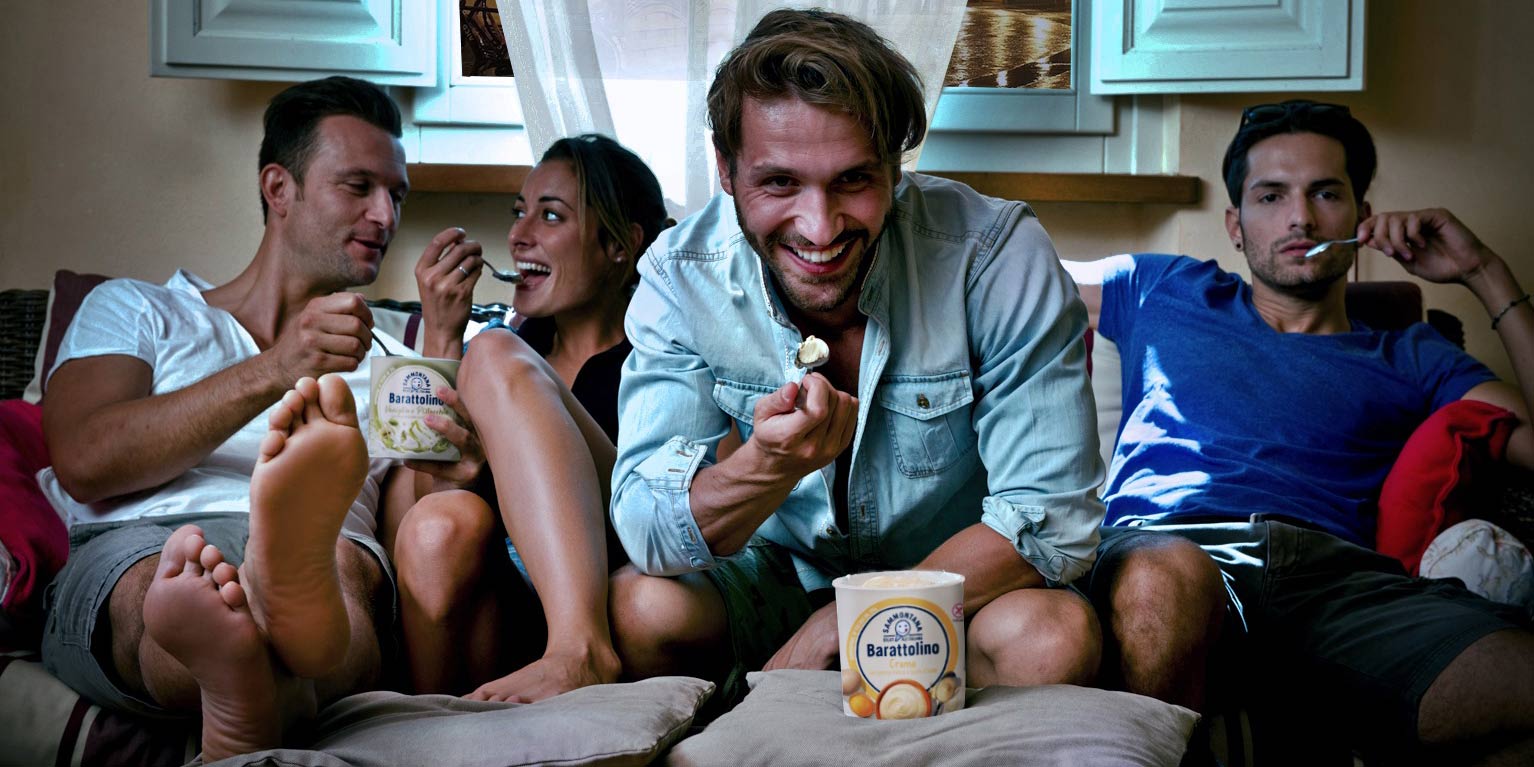
In 2005, we started working in the plants of Empoli and Vinci to fulfill the traceability of finished products, then in 2007 we extended the functionalities of the WMS to the management of feedstock. Subsequently, we have implemented since 2010 the WMS in the 4 production plants for the management of both raw materials and finished product. The last two major steps we have taken are related to the new logistics hub in Montelupo (FI), next to Empoli, opened in 2013, with the implementation of the Delivery module for transport planning too. We have automated the printing of the DDT on A4 sheet and implemented digital signature and QR Code to allow the delivery person to directly report the delivery with their smartphone.
Gabriele Calugi
IT Manager Sammontana.
Goals
- Increase warehouse productivity and accuracy
- Making work in cold storage more efficient
- Traceability Management
- Reducing fulfillment time
- Reducing picking errors
- Increased level of customer service
- Unification of logistics systems
Installed products
- WMS: StockSystem
- Add-on WMS: SMA.I.L:) Voice
- add-on WMS: SMA.I.L:) Delivery
- Voice hardware: 32 Talkman terminals T2X and T5 and A720
- Hand-held hardware: 64 Honeywell freezer terminals
- Hand-held hardware: 106 Honeywell hand-held terminals