Case History
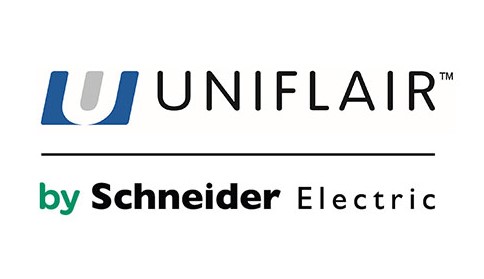
Viale della Tecnica, 2, 35026 - Conselve - PD
+39 049 5388211
+39 049 5388212
www.schneider-electric.com
Uniflair Spa
Mechanical industry, Electrical & Electronics
Since 1988, Uniflair has specialized in the design, manufacture and marketing of precision air conditioners, refrigeration systems and raised floors that have the specific function of providing advanced and reliable technological solutions for construction, Telecom-Internet systems and industrial refrigeration and comfort.
Starting with the domestic market, Uniflair's expansion has reached Europe and other continents. It is currently present in more than 60 countries around the world with its own facilities and through selected partners.
The Uniflair organization is articulated in the Conselve (Padua) headquarters, production and R&D site, in offices in Milan, Rome and Naples, and with subsidiaries in Spain, Germany, Hungary, South Africa, India and China.
Schneider Electric
The numbers of Schneider Electric
Schneider Electric, formerly Uniflair, specializes in the design, manufacture, and marketing of precision air conditioners, refrigeration systems, and raised floors that have the specific function of providing advanced and reliable technological solutions for buildings, Telecom-Internet systems, and industrial refrigeration and comfort.
EMPLOYEES
PRODUCTION LINES
PRODUCTION PLANTS IN THE WORLD
AND MORE COUNTRIES
Logistics Experience
CONSELVE (PD) PLANT
- 16,000 m2 production area
- 14 production lines
- 6500 pallet places
- 1000 m2 of racking
PLANTS IN THE WORLD - St. Louis R&D Center (USA)
- Costa Mesa Plant (USA)
- Bangalore Plant R&D Center (INDIA)
- Zhuhai (China)
- Shanghai R&D Center - China