Case History
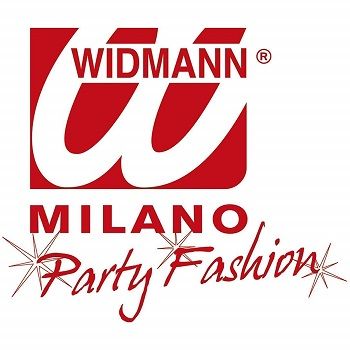
Viale dell’Industria, 3/C, 20020 - Busto Garolfo - MI
+39 0331 560001
+39 0331 537565
www.widmannsrl.com
Widmann Srl
Textile & Fashion, Utilities, Services & Other Sectors
Widmann is a leading European company operating in the import/export of party and entertainment items: costumes, wigs, decorations and accessories for Halloween, Christmas, New Year, Carnival and Parties.
Widmann Srl
Widmann's numbers
Widmann is a leading European company operating in the import/export of party and entertainment items: costumes, wigs, decorations and accessories for Halloween, Christmas, New Year, Carnival and Parties.
AND MORE YEARS OF EXPERIENCE
PRODUCTS
EMPLOYEES AND AGENTS
SQM WAREHOUSE
Logistics Experience
Radio frequency hardware store management software with Voice and Picl2LightAir
Busto Garolfo Headquarters
- 20,000 m2 total surface area
- more than 20 product lines handled
- storage capacity of 50,000 pallets