Case History
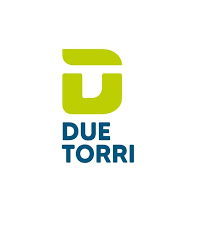
Via Maceri Superiore, 16/a
40061 - Minerbio
Tel: +39 051 6619011
Due Torri Spa
Logistics & Transportation
Due Torri Spa is an Italian company founded in 1974 that has been in the business of integrated logistics for over 35 years. It has 15,000 square meters of covered warehouses, 6,000 square meters of temperature-controlled warehouses (8-30°C), cold rooms (of 2-8°C), 4,000 square meters of customs area.
It employs about 150 people to manage all warehouse activities and processes, all distribution activities and flows, the implementation of customized and personalized logistics services for all its customers.
Integrated technologies:
Due Torri SPA
Due Torri's numbers
Due Torri is a leading benchmark for those seeking reliable, flexible and secure integrated logistics services.
WAREHOUSES
AND MORE EMPLOYEES
SQM OF WAREHOUSE OF WHICH 8,000 AT CONTROLLED TEMPERATURE
For more than 35 years we have been operating in integrated logistics handling goods of all kinds: biomedical, cosmetics, apparel, pharmaceutical and veterinary, publishing, lighting, dry food, tax and vat warehouses, and with Replica Sistemi's StockSystem, we have optimized the operation of all logistics activities and improved the service offered to our customers.
Claudio Franceschelli
President Due Torri Spa
Due Torri stands as General Contractor:
- manages all phases of the process (inbound, warehousing, outbound)
- manages, coordinates and monitors resources
- provides a single interface through customer service
- ensures compliance with compliance and regulations
- provides 360-degree service to foster client success
- ensures service and reliability for their client's customers as well
- in outsourcing, it guarantees a compliant warehouse
- in house, offers solutions for process optimization