Case History

Via Provinciale 5/7/9, 83030 - Manocalzati - AV
Tel: +39 0825 620111
info@capaldo.it
portale.capaldo.it
Antonio Capaldo Spa
Hardware & Plumbing
The company was founded in 1935 in Atripalda, where it retained its registered office until July 2013, when the registered office was merged with the operations office in Manocalzati.
In 1984 the only operational headquarters was moved to the neighboring territory of the municipality of Manocalzati, in a newly built complex consisting of two large warehouses with an office building and large parking lots.
Subsequent expansions carried out in the years 1992-1994 and 2000-2001 made it possible to reach the current size of the complex, which stands on a property area of about 80,000 square meters within which buildings for more than 40,000 square meters covered continue.
The need to rationalize and strengthen the company's logistics prompted the realization of an automated plant: and so in the years 2006-2009, a set of warehouses capable of housing goods for a total volume of 400,000 cubic meters was built in the Avellino Industrial Nucleus - Santorelli locality - on a property area of about 70,000 square meters.
The automated warehouse dedicated to pallets holds as many as 40,000 and is 33 meters high. Similarly, over the years, the range of goods has been enriched. To the initial and classic "Hardware and Colors " soon were added " plate glass " ( long since discontinued ) and then other product categories.
Logistics Experience
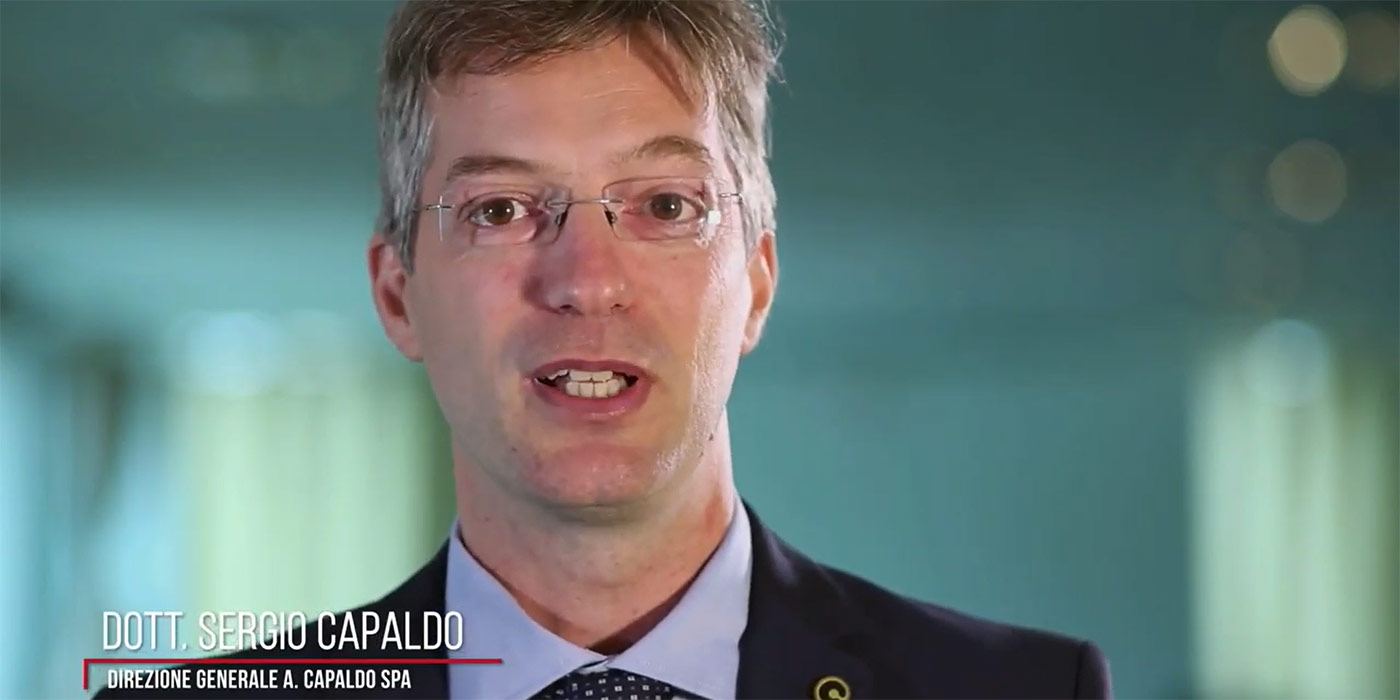
Logistics Experience - A. Capaldo
Interview with Sergio Capaldo
A. Capaldo SpA
A. Capaldo SpA Numbers
A. Capaldo Spa, founded in Atripalta (AV) in 1935, is the current Italian leader in the distribution of hardware tools, building products, garden furniture etc.
SQUARE METERS WAREHOUSE
MANAGED REFERENCES
PALLET SPOTS
STORED PALLETS PER HOUR
STORED BOXES PER HOUR
STORAGE BOXES
NEEDS
In 2005 there were 18,000 catalog items ranging from small parts to bulky items supplied by more than 1,000 domestic and foreign suppliers for a total handling of 600 TEUs/year.
Approximately 200 deliveries were processed daily to a total of over 3,000 active customers who were also guaranteed repair service. Storage was done in the traditional way and warehouse management was with "pen and paper."
The main issues were:
- complex warehouses with widely varying product types;
- diversified warehouses:
- two retail warehouses totaling 10,000 square meters for picking and wholesale;
- a 40,000-square-meter warehouse for picking and proximity stock;
- a warehouse with 40,000 pallet spaces for off-season stock and material reserve;
- an 8,000-square-meter warehouse for stock management;
- operational inefficiencies in the warehouse;
- research into software solutions for managing all warehouse activities.
SOLUTIONS
Capaldo's Executive Management became aware of some warehouse operational inefficiencies and, after careful software selection, decided to entrust the StockSystem warehouse management system with the management of all operational and decision-making activities.
The company then implemented the StockSystem solution in the standard version, with RF terminals that enables real-time data transmission to the warehouse management system. Logistics operators work efficiently using RF (Radio Frequency) terminals interfaced with remote Access Point repeaters.
The goals were:
- growth: in terms of both the number of references handled and volumes;
- reduction of errors;
- increased productivity and reduced lead time;
- increased operational flexibility (management of customizations);
- real-time handling and "everywhere" information;
- certainty of timing and operators;
- timely management of replenishment between warehouses;
- timely management of replenishment between locations in the same warehouse;
- real-time warehouse queries;
- traceability of materials;
- efficiency in the use of warehouse space;
- simplifications in rotating inventory management.
StockSystem initially interfaced with the AS/400 ERP already in use by the company and having noted the professionalism of the Replica Sistemi team decided to change partners for the information system and rely on Replica Sistemi for ERP management as well.