Case History
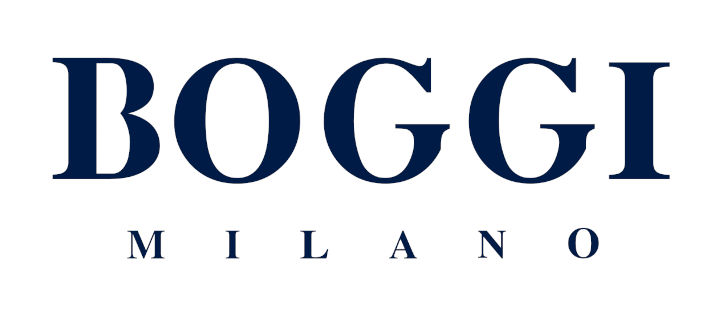
Via Borsa, 23,
20900 - Monza - MB
+39 039 596411
BBB Spa - Boggi Milano
Textile & Fashion
Since 1939 Boggi Milano, menswear brand, designs and designs contemporary men's fashion, taking care of every aspect from production to distribution.
Logistics Experience
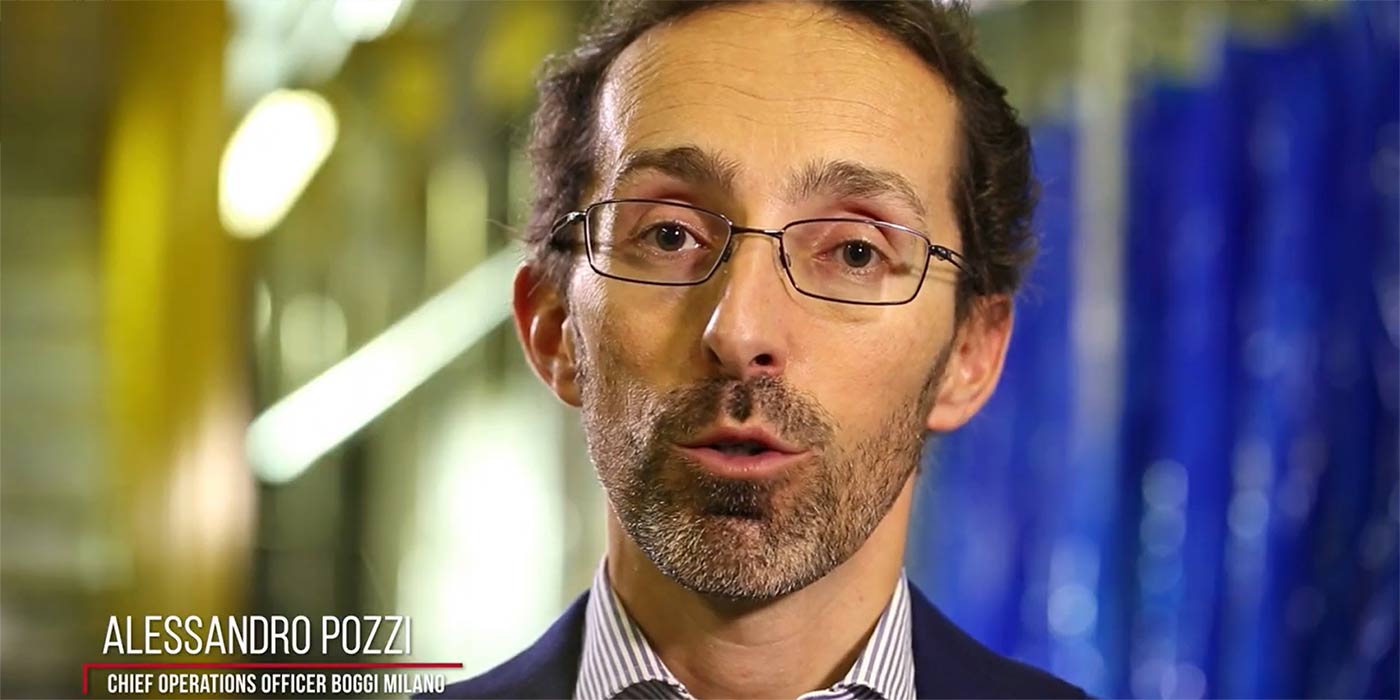
Logistics Experience - Boggi
Interview with Alessandro Pozzi
Boggi Milano
Boggi's Numbers
Since 1939 Boggi Milano, menswear brand, designs and designs contemporary men's fashion, taking care of every aspect from production to distribution.
SQUARED METERS SURFACE
STORES GLOBALLY
GARMENTS DELIVERED PER YEAR
Company
Boggi Milano is acknowledged as the epitome of passion for Italian elegance and as one of the most important menswear companies.
Founded in 1939, Boggi Milano caters to the cosmopolitan man with a suitable offer for all occasions.
The philosophy of Boggi Milano is distinguished by some fundamental values on which its international success is based: passion, elegance, tradition and quality.
With more than 190 stores in more than 38 countries, the brand is constantly expanding globally and aims to spread its style across borders, always focusing on the peculiarities of markets and people.
The logistics warehouse
The 8,000-square-meter warehouse is divided into 3 floors of hanging product and 4 floors of laid product, and a 1,500-square-meter area designated for cross-docking.