Case History
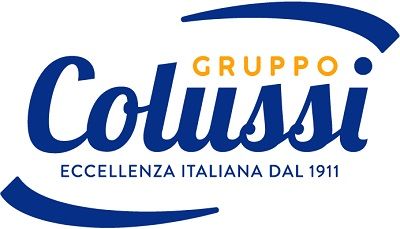
Colussi Spa
Food & Beverage
Colussi Group brings together some of the best-known brands in the Italian food tradition - Colussi, Gariboldi 1889, Misura, Agnesi, Flora, Sapori di Siena 1832 - and distributes two leading international brands - Liebeg and Del Monte.
Virtuous brands, selection of excellence and representatives of Made in Italy throughout the world.
Each of the Group's brands expresses the values encapsulated in Colussi's DNA: the great Italian food tradition, quality as the guiding star, innovation as research, development and dynamism, integrity in action, and respect for consumers, customers, and collaborators.
Colussi Group
Colussi Group's numbers
Colussi Group is a private Italian business enterprise operating in the food sector.
Its activities include the production and marketing of a full range of high-quality products: pasta, rice, baked goods, and pastries.
PRODUCT AREAS
PRODUCTION SITES
EMPLOYEES
MAIN MANAGED BRANDS
Company
Watch the video
Colussi Group is a private Italian entrepreneurial reality operating in the food sector.
Starting from the small artisan workshop founded in 1911, and leveraging the constant pursuit of excellence, it has become a solid enterprise that diversifies its activities in the quality food sector, successfully competing in major European markets.