Case History
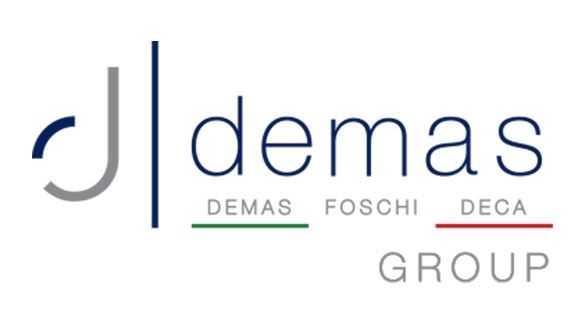
Demas Srl
Chemical, Pharmaceutical & Medical, Petfood, Pharma & Accessories
Demas was founded in 1968 with a distinctly zootechnical spirit to meet the needs of the time.
Over the years, it has grown from a small local business to serve the entire national and international territory today, dedicating itself to different professional figures, introducing the company to the entire field.
In recent years, thanks to the sensitivity of the management always attentive to the needs of the market, it is positioned in Italy as a leading company in the distribution of zootechnical medicines.
Integrated technologies:
Logistics Experience
Watch the video
Breeders, Wholesalers, Veterinarians, Pet Stores, Pharmacies, Stables and many others are served, managing to meet each and every need in the best possible way. In addition, DEMAS with Giulius - the friend of animals - in its stores is also retailing and makes available to veterinarians, breeders and private individuals more than 27,000 references in veterinary medicines, feed and supplements, and instrumental equipment.