Case History
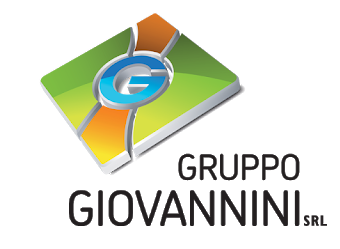
Via di Campotrentino, 50
38121 - Trento
Tel: +39 0461 404000
http://www.gruppogiovannini.com
Gruppo Giovannini Srl
Electrical & Electronics
Gruppo Giovannini
Gruppo Giovannini's numbers
Gruppo Giovannini is well established throughout the Northeast and is one of Italy's leading distributors in the electrical wholesale industry.
OPERATING SITES
LOGISTIC HUB
SQUARE METERS COVERED LOGISTICS HUB
HOME & LIGHT STORE
CORPORATE STRUCTURE
Gruppo Giovannini includes:
- Giovannini Materiali Elettrici s.r.l.
- ME.TA. COMMERCIALE Materiali Elettrici s.r.l.
- CEA Materiali Elettrici s.r.l.
- MEL Materiali Elettrici s.r.l.
- Electro Self Materiali Elettrici s.r.l.