Case History

Via dell'Adige, 2/1, 39040 - Cortaccia - BZ
Tel: +39 0471 818400
info@rothoblaas.com
www.rothoblaas.com
Rotho Blaas Srl
Furniture Complements & Construction
Rotho Blaas, a leading Italian multinational in the development and supply of advanced technologies for the building industry, has had a technological partnership with Replica Sistemi for 15 years.
Rotho Blaas was established as a family company that operates globally, embodying Alpine traditions and an international outlook. Always available to customers wherever they are, the company produces specialised products and services tailored to building professionals, including carpenters, engineers, architects, and fall protection system installers. The company, which operates in over 30 countries and 70 markets, has achieved remarkable levels of delivery accuracy and punctuality. This is thanks to the WMS StockSystem, which manages the 11,700 m² warehouse, including the automated warehouse. In addition, the Controller software has enabled the company to keep a close eye on transport costs.
The company occupies a contemporary, energy-efficient edifice, made of wood and glass, with a timber and steel support structure. The building, spanning 11,700 m² of warehouse space and 7000 m² of office space, has been thoughtfully constructed to align with the company’s product range and cultivate team morale across departments. It seamlessly integrates into the surrounding environment, embodying a harmonious coexistence with nature. The new self-sustaining warehouse, made of wood and equipped with an automated system, adds nearly 5000 m² of covered space. The facility serves as an efficient warehouse for the timely replenishment of existing warehouses worldwide and those planned for the future, supporting the company’s growth.
Logistics Experience
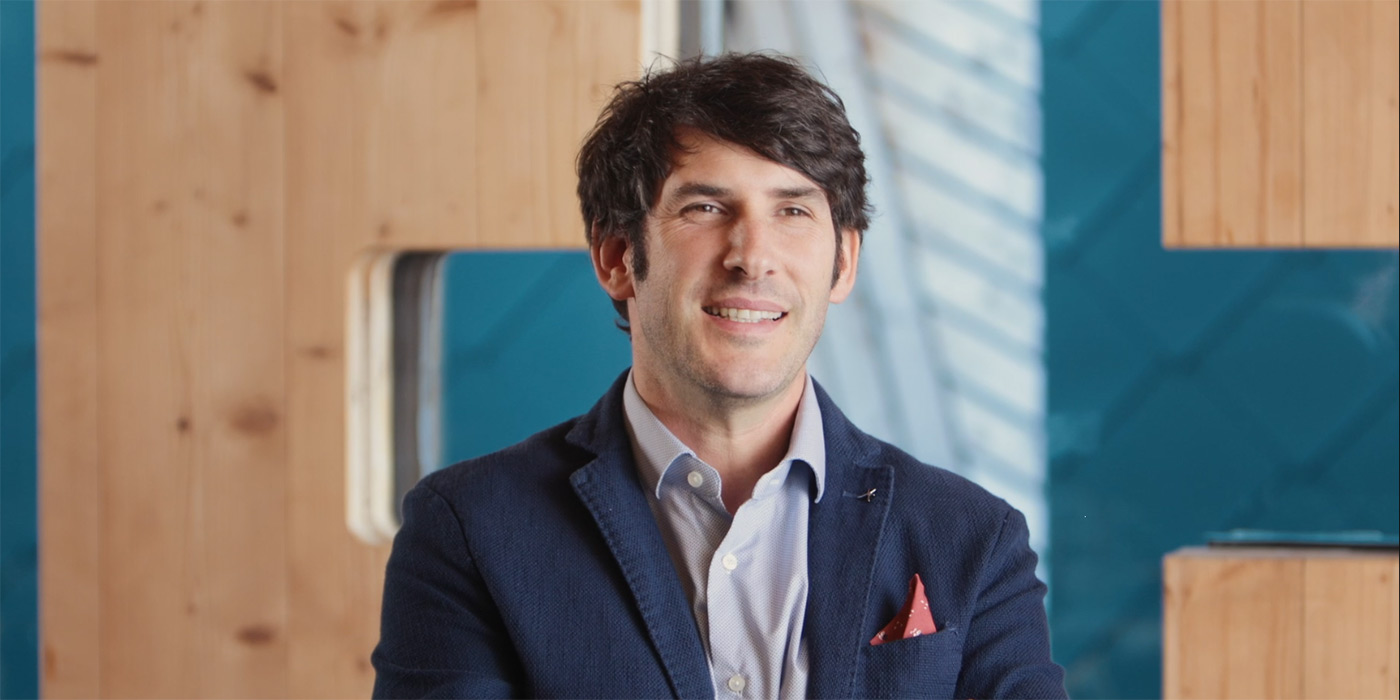
Logistics Experience - Rotho Blaas
Interview with Alexander Vaja
“We have multiple warehouses across the globe, and I believe StockSystem is the epitome of a high-performance WMS tool, like a Ferrari for warehouse management.”
Alexander Vaja
Logistics & Transportation Director Rotho Blaas
Rotho Blaas
Rotho Blaas' numbers
EMPLOYEES IN THE WORLD
SUBSIDIARIES IN THE WORLD
STORAGE SITES IN THE WORLD
YEARS OF EXPERIENCE
DAILY SHIPMENTS
COUNTRIES IN THE WORLD
Collaboration Steps
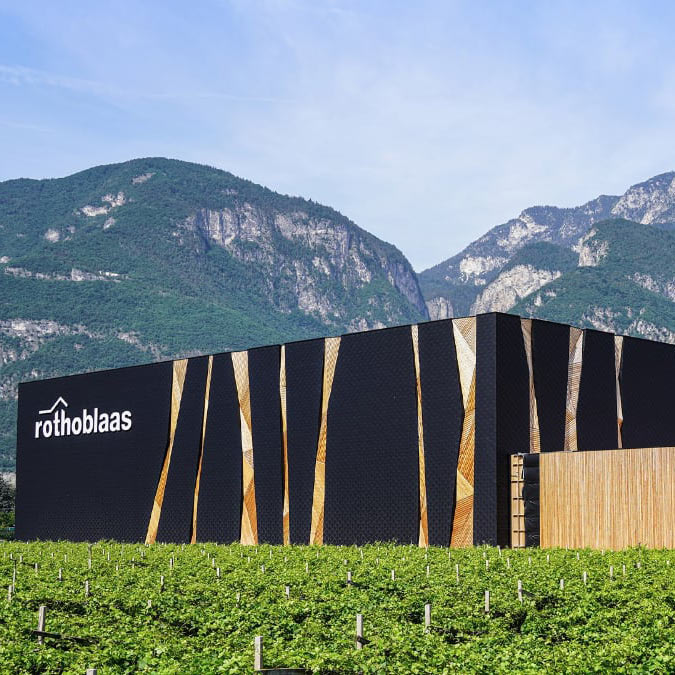
- 2008: Go Live StockSystem
- 2011: Major Release StockSystemEvolution
- 2019: Implementation of TMS Controller
- 2022: Integration of WMS StockSystemEvolution with the automated warehouse
- 2023: Implementation of WMS StockSystemEvolution in Spain and integration of TMS Controller with WMS StockSystemEvolution in Spain
The Softwares
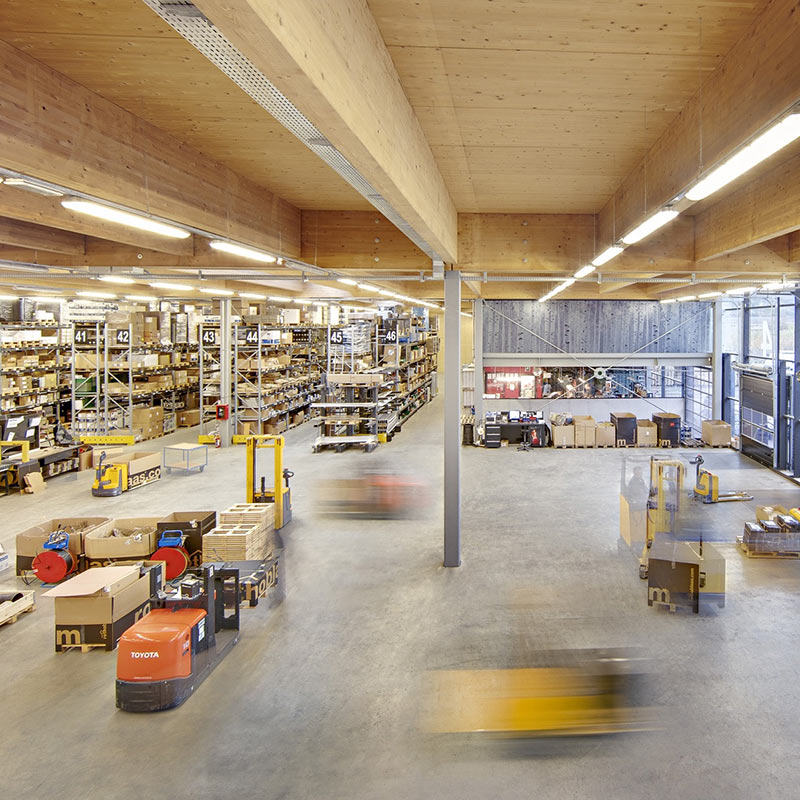
In addition to integrating with Controller, StockSystem in Italy also communicates with other company software.
This includes the company’s ERP COMARCH, the QS1 software for quality control and, starting in 2022, AWM - the software responsible for operating the automatic warehouse, an impressive structure comprised entirely of laminated wood shelves containing four stacker cranes and special robots that move efficiently within. This sustainable system has had a significant impact on productivity and is the first and only one of its kind in Italy.
Managed Flows with Integrated WMS and TMS
Thanks to the collaboration with Replica Sistemi, the current activities have been successfully managed:
- COMARCH ERP system transmits sales orders to Stocksystem to manage the picking process;
- StockSystem WMS dispatches shipments to Controller for the selection of the most suitable carrier;
- StockSystem WMS dispatches picking tasks to the operators and liaises with the automated warehouse to retrieve materiel, if required;
- Controller TMS sends the most suitable carrier to Stock system;
- After completing the picking process, the warehouse operator verifies or modifies the carrier selection and informs Controller;
- Shipment occurs with all appropriate transport documentation;
- Controller checks the invoices received from the carriers;
- Controller sends COMARCH ERP reports highlighting any irregularities.
Benefits of Integration
- Piloting and harmonising logistics flows within the warehouse to boost efficiency for each process based on carrier, weight, ADR content, voluminous content, and urgencies;
- Reducing costs and errors by selecting the most convenient carrier ultimately lead to increased margins;
- Automatic auditing of carrier invoices;
- Automated invoice resolution allowing analytical cost centre allocation;
- Complete integration of data and information flow with corporate software and external partners localised in Italy and Spain;
- Analysing reliable and shared data useful for the elaboration of KPIs.