Case History
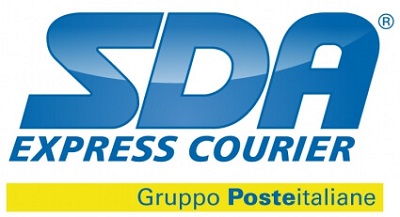
SDA Express Courier
Logistics & Transportation
SDA Express Courier (formerly Italia Logistica) is born from the union between SDA Logistica (SDA Express Courier - Gruppo Poste Italiane) and Omnia Logistica (FS Logistica - Gruppo Ferrovie dello Stato), which put their experience together to create this great enterprise. It's a company that wants to bring significant change in the fields of integrated logistics, multimodal transport and document management.
Thanks to the combined experience and reliability of the two original groups, SDA offers a wide range of services with high added value, and through the help of evolved information systems they are able to satisfy any need: from integrated logistics to overseas transport, from staging to retail/large distribution delivery, not to mention e-procurement, binding, technical courier.
SDA Express Courier can count on a widespread network that covers the entire national territory, composed of 22 logistic platforms (200,000 sqm) and a daily road network.
SDA Express Courier
The numbers of SDA Express Courier
SDA Express Courier – part of the Poste Italiane Group – was born in 1984 and stands as a leading Italian company for logistics and BtoB distribution management, offering a wide range of services to cater to any shipment request: from standard express services, to integrated logistics ones, from technical couriers to technological solutions for e-commerce.
SUBSIDIARIES IN ITALY
LOGISTIC PLATFORMS
MILLIONS PACKAGES/YEAR
AND MORE EMPLOYEES/COLLABORATORS
Facilities
NUMBERS OF THE GORGONZOLA LOGISTICS PLANT
- 8,000 squared meters of covered surface
- 10,500 available pallet spots
- around 1,600,000 packages sent per year
- over 2,000,000 orders executed per year