EasYard, is the web-based Yard Management System (YMS) solution of the SMA.I.L:) platform.
It manages all activities taking place within the yards, optimizing inbound and outbound processes.
The YMS enables the management and control of vehicles, goods and people entering, stopping and leaving yards.
Integrated with license plate recognition technologies and vehicle registration and weighing totems, the software can track movements within plants.
Features
EasYard is the Yard Management System, designed for the management and control of vehicles, goods and people entering, stopping and leaving yards.
The YMS enables a reduction in driver waiting time and related costs for performing loading and unloading activities with warehouse slot booking.
It provides a real-time view of activities in the yards, allowing better planning of warehouse activities as well.
Optimizes available resources with a loading and unloading schedule that synchronizes warehouse and yard receptive capacity with vehicle arrival reservations within plants.
Helps prevent accidents and damage to goods through visual control of vehicles entering, standing in the yard, moving in and out of the company.
Features
Security and efficiency
in every step of the
Supply Chain
Integrated with security management tools for managing automatic access control, body temperature detection and social distancing, it ensures safety and efficiency at all stages of the Supply Chain.Complete digitization of yard logistics access reduces waiting time for drivers, avoiding queues and gatherings.
How does Replica Sistemi's EasYard YMS work?
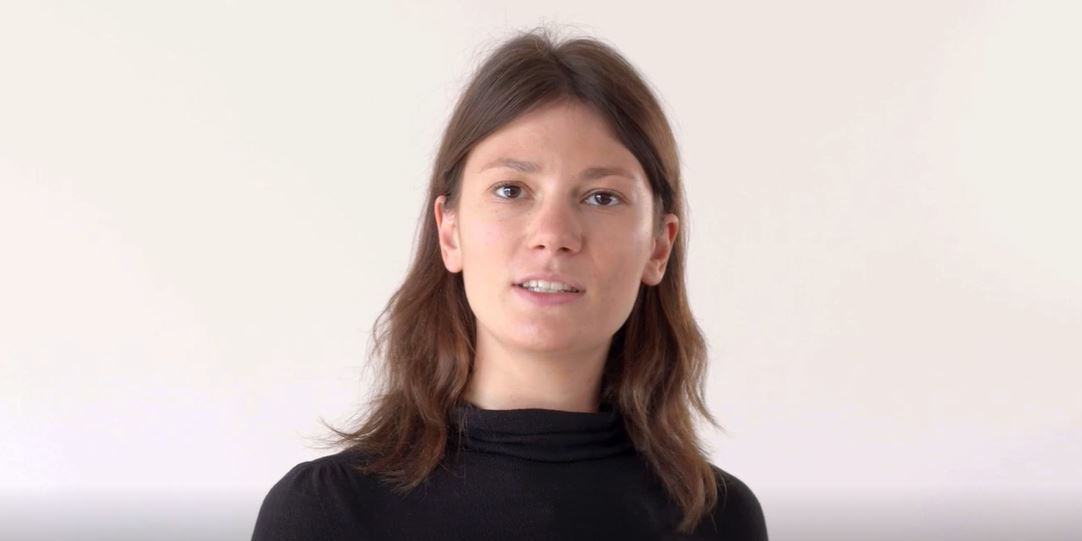
Video tutorial EasYard
In this video tutorial, some Replica Sistemi project managers explain how the YMS works
The main processes managed by the Yard Management System - Security Management System EasYard:
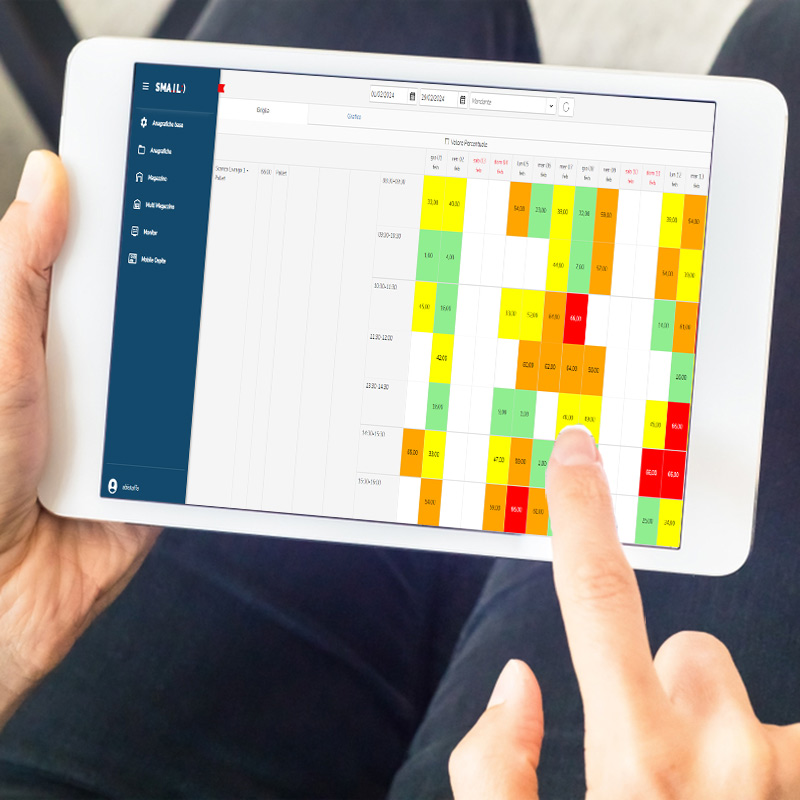
Time Slot Management - Warehouse slot booking
The YMS automates delivery appointments, reducing time and procedures and decreasing empty trips with the warehouse slot booking.
Suppliers, customers and transporters can book themselves for loading/unloading activities at the warehouse on available days/hours.
The system allows:
- Inserting availability for configured slots.
- Loading of bookable orders into the system.
- The supplier receives the order; the carrier (or supplier) books himself for the requested delivery.
- The carrier provides all the necessary information to finalise the booking in the system.
- The system monitors the booking schedule in real time and, if necessary, asks for any changes.
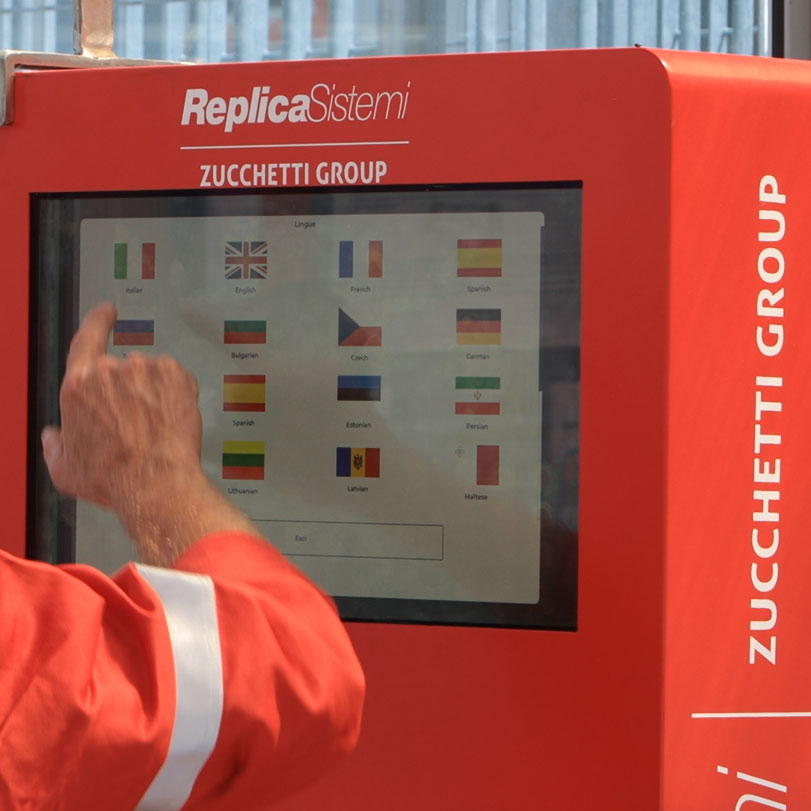
Self Check-in and Registration
Integration with registration totems enabling:
- Self registration of drivers 24/7 with multilingual interface.
- Possible customization of screens and information.
- Compatibility check with orders/customers/suppliers/gate.
- Tracking and tracing of all drivers who have passed the safety course and are thus authorized to access the plant.
A quickly and easily configurable safety course is available from registration totems or by sending a link via text message directly to the driver. Flexible questions and quick management of the end result. After reading the document-video on safety, the driver must correctly answer the test questions that are proposed on the following pages. In case of wrong answers, the driver has the option to view the safety course again and retake the test or take the test directly.
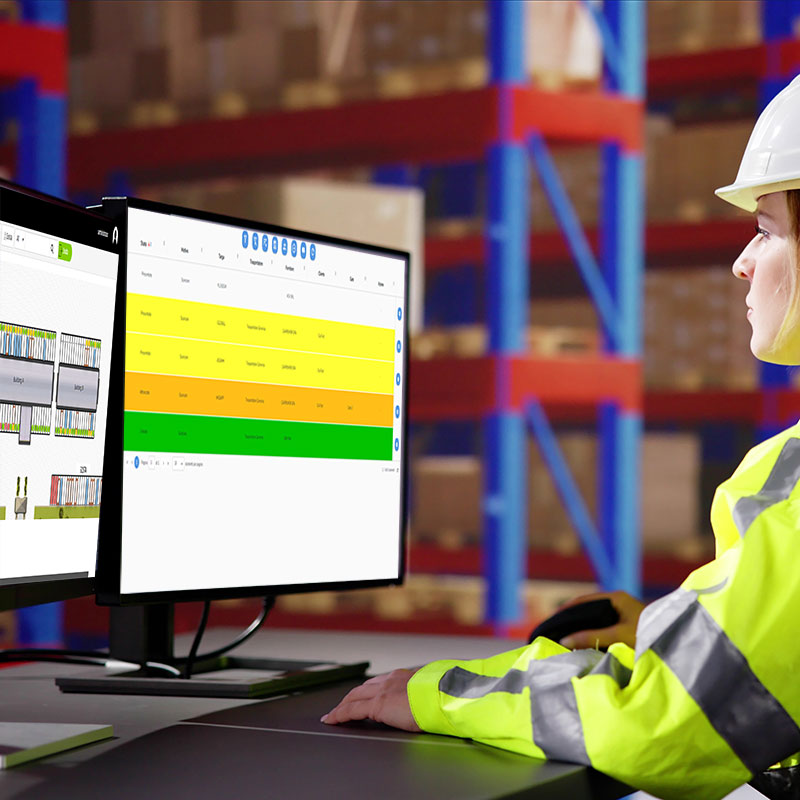
Yard Management
- Immediate visualization available on any device of the state of the art of vehicles waiting, being loaded/unloaded or exiting the plant.
- SMS/E-mail service, translated into the spoken language, for direct communication to drivers and visitors of actions to be taken.
- Tracking of vehicle movement.
- Detection of handling times.
- Configuration of the operational workflow, in order to allow the hesitation of the activities of the different offices as they are handled.
- Automatic rules management for alert activation and enabling means and/or person to enter/exit the plant.
Field technologies
The yard management system which integrates with different
field technologies.
The EasYard yard management system allows dynamic management of incoming vehicles; integration with access control system allows automation and speeding up check-in and check-out activities at the gatehouse. Thanks to integration with document archiving systems, in real time it is possible to consult and analyze on one's own devices the vehicles in the plant. Integration with vehicle weighing systems , allows the driver to never have to get out of the truck, ensuring greater safety.
Advantages of EasYard
Efficiency
- Minimisation of drivers' waiting times and related costs for loading and unloading activities.
- Minimisation of manual input and data checking activities by supervisory staff.
Safety
- Helps preventing accidents and damage to goods through visual inspection of vehicles entering, stopping in the yard, moving in and out of the company.
- Certification of compliance with plant safety regulations.
Control
- Helps preventing accidents and damage to goods through visual inspection of vehicles entering, stopping in the yard, moving in and out of the company.
- Certification of compliance with plant safety regulations.
Productivity
- It optimises the available resources with a loading and unloading schedule which synchronises the receptive capacity of the warehouse and yard together with the arrival bookings of trucks within the plants.
- Monitoring the performance of suppliers' and customers' carriers.
- Detecting inefficiencies and anomalies and developing strategies to reduce errors and recover productivity.
EasyApp, the mobile app for managing the operations of a logistics plant
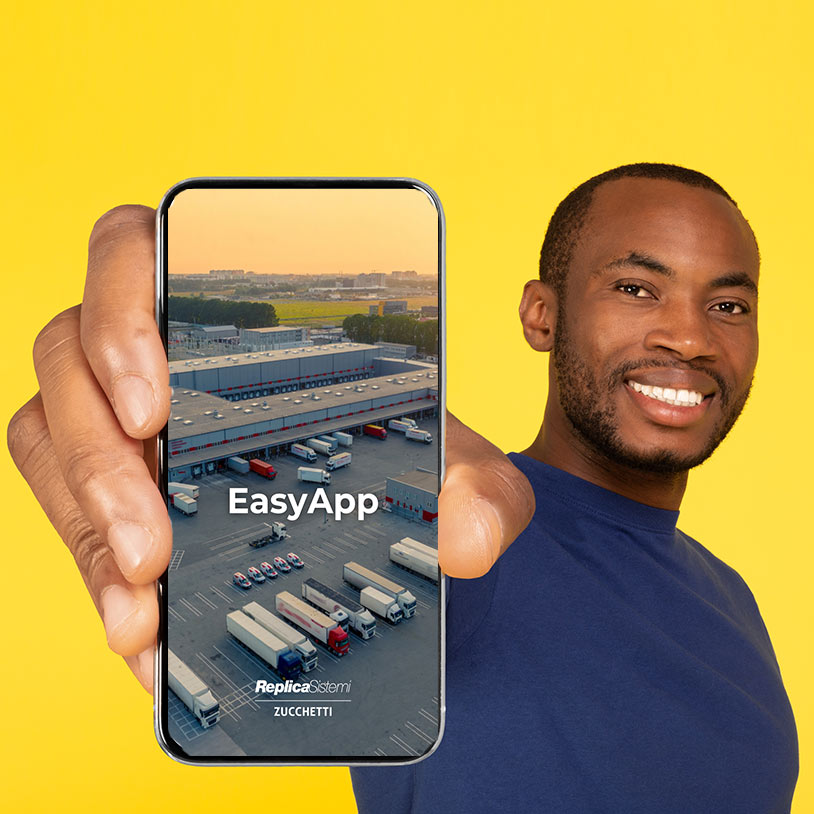
EasyApp is the mobile application of the EasYard product to have all the main functions of the yard management system at your fingertips!
It is a cross-platform app for managing Operations in an enterprise plant.
Download PDF
Information request
For any questions or information about our products or services, please do not hesitate to contact us.
Share this content on: